3 kroki do zarządzania jakością produktu — część 2 Jakość i procesy dostawców
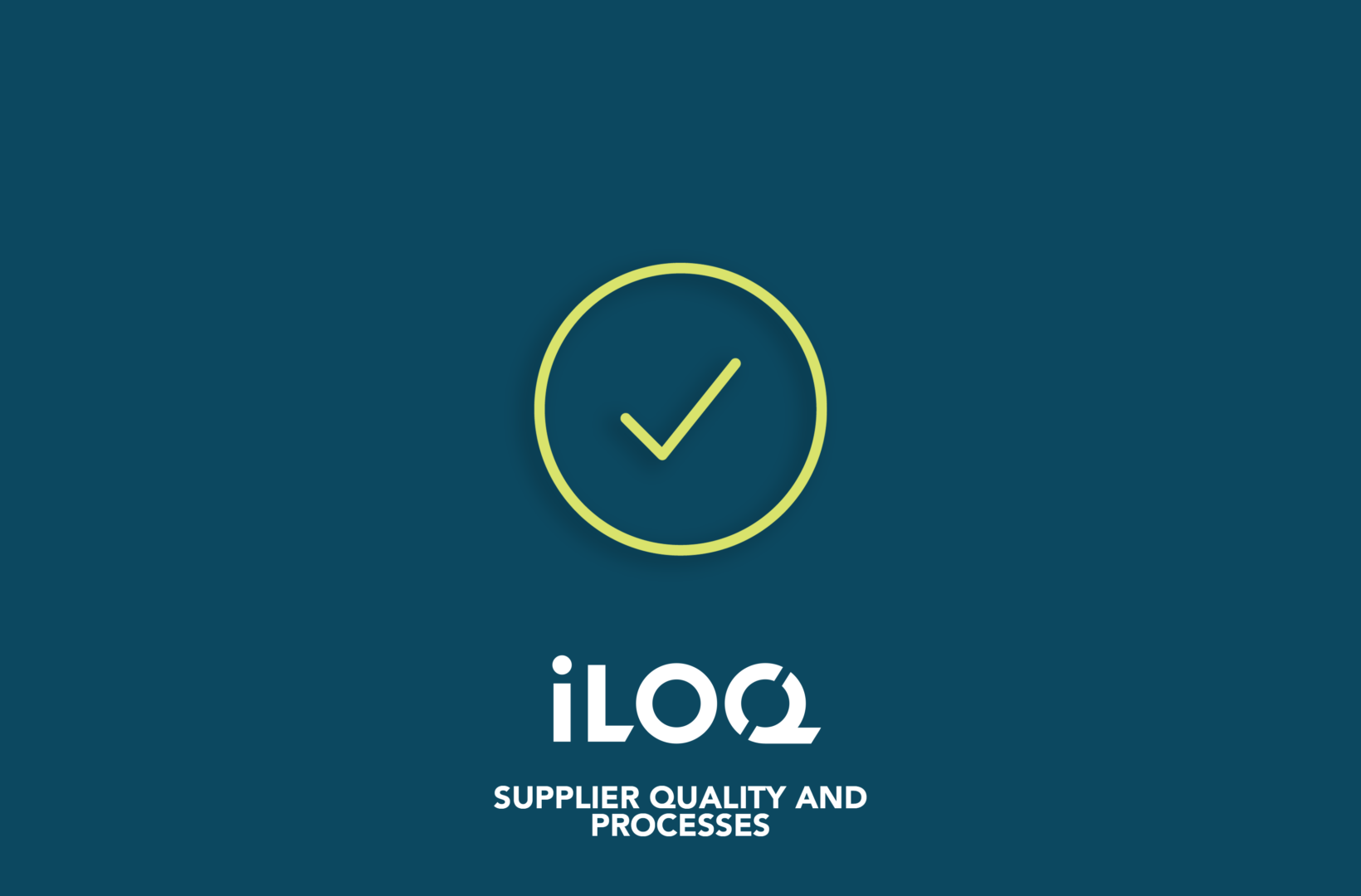
W naszym ostatnim wpisie na blogu przyjrzeliśmy się, w jaki sposób się upewniamy, że nasze produkty są projektowane z myślą o dobrej jakości i niezawodności. W tym poście przyjrzymy się jakości naszych dostawców i ich procesom. Produkcja wysoce specjalistycznych mechanizmów iLOQ wymaga znalezienia najlepszych w swojej klasie dostawców. W iLOQ postrzegamy dostawców jako partnerów wspierających nasz rozwój. Przykładamy dużą wagę do współpracy z dostawcami i przeznaczamy na nią wiele środków. Nasze procesy jakościowe spełniają wysokie standardy w połączeniu z najlepszą dostępną technologią produkcji. Projektowanie pod wytwarzanie (Design for Manufacturing, DFM), realizowane przy współpracy z zespołem inżynierów dostawcy, jest jednym z procesów realizowanych od samego początku rozwoju produktu. Jest to model projektowania części, komponentów lub wyrobów pod kątem łatwości ich wytwarzania, którego celem końcowym jest stworzenie lepszego wyrobu przy niższych kosztach. Wczesne zaangażowanie dostawców jest kluczową kwestią ku zapewnieniu, że wdrażanie nowych technologii produkcyjnych nie niesie za sobą podwyższonego ryzyka i jednocześnie będzie efektywne kosztowo. W ocenie współpracy z dostawcami stosujemy takie narzędzia statystyczne, jak wskaźnik zdolności procesu (CPK), wskaźnik wydajności czy statystyczna kontrola procesu (SPC). Są one stosowane w zarządzaniu jakością w celu zapewnienia, że proces produkcyjny spełnił limity specyfikacji określone dla danego procesu lub produktu. Aby móc produkować wysokiej klasy komponenty mechaniczne, konieczne jest wprowadzenie kontroli procesów. W iLOQ wymagamy i przestrzegamy metryk danych. Dostępność wysokiej jakości części do produkcji zamków zostaje zapewniona przez nadzór procesów produkcyjnych i wprowadzanie koniecznych korekt. Aby zapewnić najlepszą możliwie jakość, ściśle współpracujemy z naszymi dostawcami, organizując warsztaty jakościowe, bezpośrednie spotkania i regularne przeglądy. Audyty dostawców pozwalają zidentyfikować potencjalne zagrożenia dla działalności iLOQ, a także pomagają dostawcom stać się częścią naszej procedury ciągłego doskonalenia. Zatwierdzanie części Zatwierdzanie części rozpoczyna się od dokumentacji, która jest wysyłana do dostawcy. Dokumentacja ta informuje dostawców o naszych wymaganiach i zawiera np. rysunki, wymagania jakościowe i modele 3D. Dysponując tymi informacjami, dostawcy przygotowują dokumenty dotyczące jakości części, takie jak analiza przyczyn i skutków wad procesu, plany kontroli jakości, wykresy przepływu produkcji oraz badania powtarzalności i odtwarzalności pomiarów. Otrzymujemy również procesy projektowania pod wytwarzanie do wglądu. Jeśli wszystko jest na akceptowalnym poziomie, rozpoczynają się próby produkcji pierwszych części. Te zostają poddane przeglądowi i pomiarom przy użyciu metod wstępnej kontroli jakości (FAI) oraz oceny wzrokowej. Przeprowadzane są również próby CPK. Jeśli część jest w dobrym stanie, zostają wykonane różne próby w zależności od materiału i funkcji części. Mogą one obejmować próby chemiczne, testy środowiskowe czy badania powłoki i materiału. Funkcjonalność jest również testowana na poziomie montażu. Wszystkie te ważne etapy zatwierdzania są zaplanowane w taki sposób, aby zapobiec ewentualnym problemom po stronie klienta. Kiedy wszystkie testy zakończą się pozytywnie i wszystkie parametry będą prawidłowe, dostawca otrzymuje zatwierdzenie części i może rozpocząć produkcję masową. Testy badawczo-rozwojowe i projektowanie w oparciu o testy Testowanie jest istotną częścią procesu projektowania nowych produktów. Zazwyczaj faza rozwoju produktu obejmuje kilka cykli iteracyjnych, które krok po kroku przybliżają produkt do jego ukończenia. Podczas każdej iteracji testujemy prototypy i na podstawie analizy wyników wracamy do deski kreślarskiej, aby ulepszyć projekt. Pozwala to na przystąpienie do kolejnego etapu tworzenia prototypu z ulepszonym projektem. Oprócz normalnych testów funkcjonalności w fazie rozwoju przeprowadza się jeszcze wiele innych prób. Projektując elektronikę, testujemy np. pobór mocy czy ochronę przed ESD. Przy projektowaniu układów mechanicznych zwykle testujemy trwałość poprzez otwieranie zamków 200 000 razy, poddajemy je obciążeniom środowiskowym, w tym mgle solnej, przeprowadzamy test 85/85 podwyższonej temperatury i wilgotności (gdzie produkty są wystawione na działanie temperatury 85°C i wilgotności względnej 85%) oraz przeprowadzamy różnego rodzaju ataki bezpieczeństwa i testy ochrony przed manipulacją. Musimy również zbadać integralność całego systemu, w tym komunikację i funkcjonalność, szyfrowanie, przesyłanie wiadomości itp. W ramach tych testów wybrani klienci mają szansę wypróbować nowe produkty i przekazać swoje spostrzeżenia działowi badań i rozwoju firmy iLOQ. Ustalenia te są zazwyczaj wykorzystywane w ostatnim cyklu rozwoju do określenia, czy coś jeszcze trzeba zmienić, zanim produkt trafi do produkcji. Faza produkcji nie oznacza zakończenia procedur testowych w iLOQ. Teraz charakter badań przechodzi od rozwoju produktu do testowania niezawodności w czasie rzeczywistym podczas produkcji. Pomiary części Aby zapewnić wysoką jakość naszych produktów, musimy mieć pewność, że stosowane części spełniają ustalone wymagania i specyfikacje. Do tego celu używamy szerokiej gamy urządzeń i zawsze staramy się znaleźć najlepszy i najbardziej niezawodny sposób pomiaru części. Nasze narzędzia są zróżnicowane: od podstawowych suwmiarek i mikrometrów, poprzez sprawdziany trzpieniowe gwintowe, po optyczne i współrzędnościowe maszyny pomiarowe i maszyny do pomiaru twardości i chropowatości powierzchni. W niektórych przypadkach używamy również precyzyjnych narzędzi niestandardowych. Wszystkie nasze przyrządy są kalibrowane, kontrolowane i regularnie konserwowane, aby mieć pewność dokładności pomiarów. Niektóre z naszych pomiarów części są w zasadzie pół-automatyczne, co pozwala nam na wykonanie kilku precyzyjnych pomiarów w tym samym czasie na wielu częściach. Świeżo zaprojektowane części i poprawki są kontrolowane bardziej szczegółowo, a po zatwierdzeniu części główny nacisk kładziemy na wymiary funkcjonalne i krytyczne — tzw. pomiary SPC i CPK. Dzięki temu nasze kontrole pozostają wydajne i pomagają nam skrócić czas realizacji zamówienia. Dane pomiarowe są przechowywane w systemie kontroli procesu, który umożliwia podgląd i monitorowanie zmian w czasie. Dzięki temu jesteśmy w stanie podjąć działania korygujące zanim dane części przekroczą dopuszczalne parametry. Ogólnie rzecz biorąc, jesteśmy na bieżąco ze wszystkim, co dotyczy zagadnienia pomiarów i regularnie nabywamy nowe urządzenia. Śledź nasz blog, aby dowiedzieć się więcej o tym, jak zarządzamy jakością produktów. W następnym wpisie przyjrzymy się temu, jak utrzymujemy jakość produkcji na najwyższym możliwym poziomie. I pamiętaj — jeśli masz jakieś pytania, nie wahaj się zamieścić ich w formularzu poniżej. Jesteśmy tu, aby pomóc.