3 steps to managing product quality – Part 3: Manufacturing quality
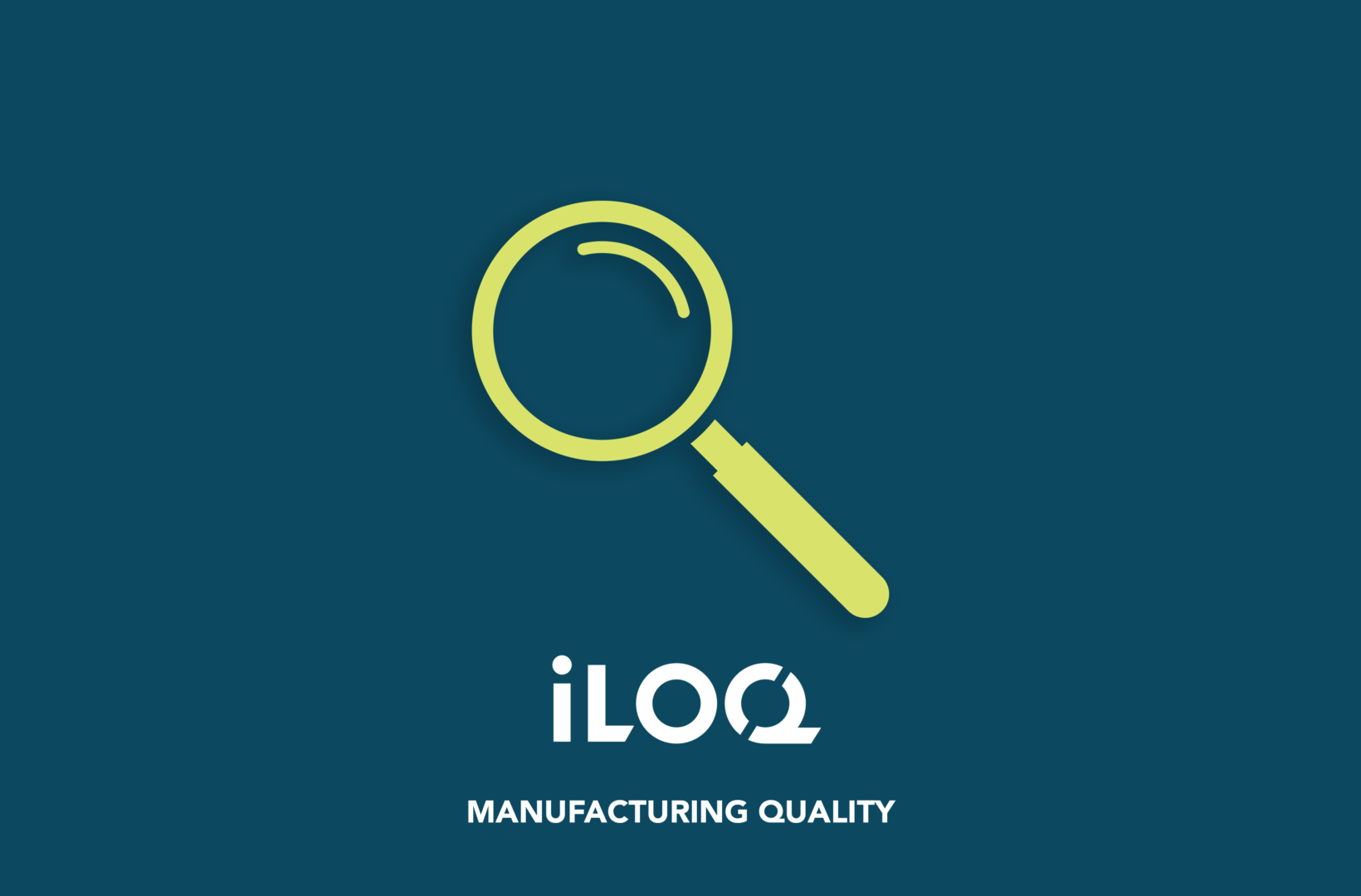
In our last blog post, we took a look at how finding best-in-class suppliers is vital to support our growth. In this post, we’ll take a look at the importance of testing to ensure the quality of our manufacturing methods.
A New Product Introduction (NPI) program encompasses all the activities within an organization to define, develop and launch a new or improved product. iLOQ’s NPI team is responsible for ensuring that new products meet our strict manufacturability and quality targets.
Manufacturing competence building typically starts early in the product development phase. We define production and R&D testing requirements and build testing capability to ensure high end-product quality in the volume manufacturing phase.
In the prototyping phase, iLOQ verifies new product quality, and planned product and manufacturing quality assurance practices. In order to build manufacturing and quality competence proactively to be well prepared for volume manufacturing, the necessary manufacturing operator trainings start in parallel for iLOQ employees and also for our manufacturing partners.
Final production start acceptance happens by making a special trial manufacturing which has to be approved by iLOQ R&D and operations before volume manufacturing can commence. The criteria and processes are the same for the whole iLOQ supply chain, including suppliers and partners.
Production testing
At iLOQ, we place a high emphasis on production testing to ensure that manufactured products meet our set requirements for functionality and quality.
As end products consist of various sub-assemblies which are put together during the assembly process, testing needs different methods that are appropriate both for the level of complexity of the sub-assembly and also for the complete assembly. The selection of the method depends on the purpose of each test step.
Generally, the early test phases are designed to catch process-related or electrical failures, or to check even minor mis-matches in, for example, component soldering. While the methods towards the end of the process aim at identifying more complex and functional defects.
New product testing
All products are first assembled on iLOQ’s own NPI line to ensure maturity before moving on to volume production, and build feedback is used to improve productivity. When moving to mass production, iLOQ’s personnel offers full support to the manufacturer by sharing assembly instructions and giving face-to-face support in first builds.
The manufacturer follows many parameters during production. For example, yields, Statistical process control (SPC), incoming quality control and outgoing quality control numbers. The most critical parameters are constantly reported to iLOQ. Close co-operation with manufacturers is vital to iLOQ. If there are any problems in production, support is promptly given.
Manufacturing testing
Typically, manufacturing testing starts with paste printing to a bare PWB board. The amount and placement of the paste in correct positions on the board is visually checked. After that, the components are placed on the PWB and soldered in an SMD oven. As soldering is very sensitive to the correct temperature profile and accuracy of component placement in the automatic placement process, the quality of the assembled PWB is visually checked again when soldering has been completed. After this, approved boards are ready for the assembly of product mechanics (a sub-assembly to a lock). As mechanical parts are physically very small, additional checks and functional tests are done during the process by a functional tester. When the tests have been successfully completed, the sub-assembly is ready to be assembled to a complete lock which will be subjected to a lock functionality test.
Lock testing is typically carried out by measuring fundamental parameters with precision instruments and checking that the lock also operates as it should. This is done hundreds of times to make sure that locks operate in different operating conditions and also in extreme temperatures.
To complement all the automatic testing in a process, locks are also manually verified by operators to ensure a good-quality and natural user experience.
This concludes our set of blog posts on the subject of how we manage and maintain the quality of our products. Make sure you bookmark our blog so that you can keep up with all the latest developments from iLOQ and within the locking industry as a whole. And, as always, don’t hesitate to post a comment in the box below if you have any questions. We’re here to help.